Production
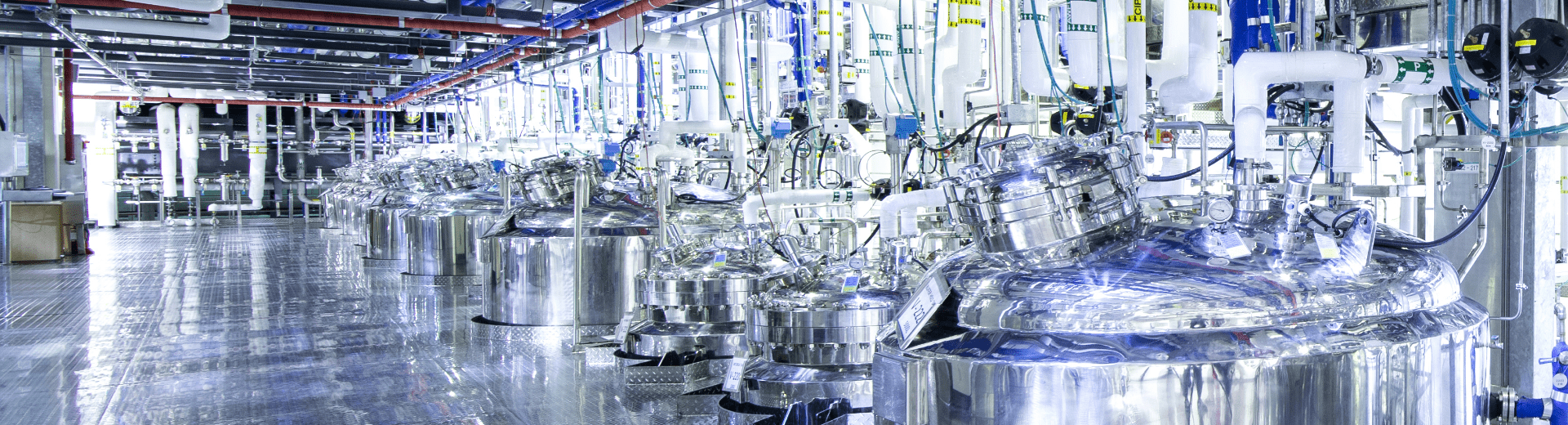
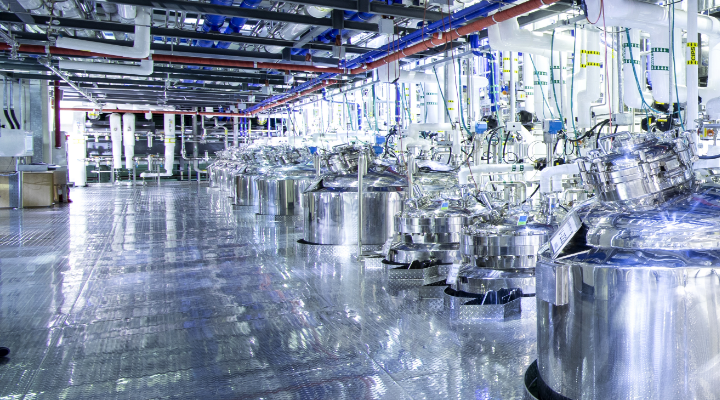
Biopharmaceutical Production Facilities
Celltrion has a production capacity of 250,000L capable of manufacturing everything from drug substances to drug products. We have acquired US FDA and Europe EMA cGMP certifications on all facilities after being the first in Asia to operate FDA cGMP certified animal cell culture facilities.
-
Plant 1100,000L 12,500L x 8 lines
-
Plant 290,000L 15,000L x 6 lines
-
Plant 360,000L 7,500L x 8 lines
Small Molecules Production Facilities
Celltrion Pharm's Cheongju Plant, a small molecule pharmaceutical development and production base for Celltrion, provides solutions for all aspects of the production and distribution of tablet and capsule formulations. It also has an FDA cGMP-certified Prefilled Syringe (PFS) production facility with a filling capacity of up to 18 million syringes per year. Go to Celltrion Pharm
Biopharmaceutical Production Process
Biopharmaceutical production process consists of cell culture process, purification process and fill and finish process.
-
Step. 01 Cell Culture Process1. Preparation of cell culture media and buffer solution
Cell culture media are nutrients essential for cell proliferation. At Celltrion, optimized media for the types and characteristics of cell lines are used and the composition and formulation ratios differ depending on the characteristics, culture method and environment. Media are as important as culture method and environment as they affect the protein productivity and quality. Buffer is a solution that is used to stabilize pH and conductivity to stably extract and purify proteins. It is one of the key factors of purification process because any changes in conditions can affect yield and product quality.
2. Cell cultureWhen cell line thawing and small-scale flask cell cultures are finished, they are gradually transferred to larger seed bioreactors as they divide and proliferate. Ultimately, cell lines produce antibodies that become raw materials for pharmaceuticals in commercial bioreactors under conditions optimized for productivity and quality.
-
Step. 02 Purification Process1. Initial purification
The initial purification process is to purify target proteins from the cell culture fluid harvested during the cell culture process. During this process, target proteins are recovered with high purity and yield through several steps of chromatography and removes viruses through virus inactivation and virus filtration.
2. Final purificationFinal purification is the process of adjusting antibody protein concentration to a level suitable for drug substance, exchanging buffers for final formulation and filtering for the last time.
3. Final filtrationAs the last step of drug substance production, final filtration is conducted to remove bacteria which leaves injectable buffer and high purity target proteins.
-
Step. 03 Fill and Finish Process1. Drug product filling and packaging
The goal of fill and finish process is filling and packaging target proteins into administrable forms. Therefore, it is operated in a thoroughly controlled “clean rooms”. Celltrion received the first-ever GMP approval from the FDA in the field of production of injectable products in Korea and operates the facilities within the FDA and EMA's GMP guidance.